Managing Supply Chain Challenges in Inventory Logistics Across Industries (PH)
.webp)
"Without logistics, the world stops." It's a fitting statement describing how vital logistics is to keeping businesses running and economies thriving. In the Philippines, managing supply chains is a daunting task. The country's geographical location, infrastructure woes, and the seasonality of goods often turn inventory logistics into a complex puzzle.
Since logistics costs are a key factor in product pricing, the need to find efficient, cost-effective solutions that reduce the burden on your bottom line without compromising quality is necessary.
Supply Chain Management Challenges in the Philippines (And How to Manage Them)
The obstacles mentioned above have a vast impact on inventory logistics management, influencing the efficiency of operations and escalating costs. If not managed, supply chain challenges can produce ripple effects — from product affordability to customer satisfaction and overall business competitiveness. Here's a closer look at the primary challenges in supply chain management:
High cost of shipping
The lack of a centralized authority to oversee the movement of goods through the country's ports has led to inefficiencies and elevated costs. These expenses often trickle down to consumers, who might not be willing to pay the fees for priority deliveries.
One way to mitigate these costs is by leveraging multi-point pickup and drop-off options to consolidate deliveries and reduce transportation distances. Localized partnerships with logistics providers also enable faster access to inventory and lower costs, ensuring a more reliable supply chain.
Complex customs processes
Lengthy customs procedures, with delays extending up to weeks, can be frustrating for businesses trying to maintain timely deliveries. Besides slowing down supply chains, inconsistent regulations and additional administrative hurdles drive up operational costs for many companies.
To address these delays, businesses can partner with third-party logistics (3PL) providers that specialize in navigating customs processes efficiently. 3PL firms provide expertise that secures faster clearances and reliable deliveries.
Port congestion and road traffic
Port congestion and heavy traffic, particularly in Metro Manila, exacerbate delays. With a congestion level of 43% and an average of 98 hours lost annually, businesses struggle to meet delivery timelines. The need for ferry services and infrastructure for crossing bodies of water further hampers inter-island trade.
Strategically placed warehouses and distribution hubs near key markets can help businesses bypass these bottlenecks. Additionally, tools that provide real-time route optimization allow for proactive adjustments, ensuring timely deliveries even in high-traffic areas.
Limited transportation infrastructure in rural areas
In rural regions, the lack of roads, bridges, and ports severely limits the movement of goods. This challenge is especially detrimental to transporting perishable goods—delays can render products unfit for consumption, causing financial losses and supply chain disruptions.
An extensive delivery network that includes rural areas ensures reliable transport of goods to even the hardest-to-reach destinations. Coupled with route optimization technology, businesses can minimize delays and maintain the integrity of time-sensitive shipments, such as perishables.
Challenges in inventory visibility across multiple locations
There are many situations or events that can disrupt transport routes and create gaps in visibility, compounding the logistical complexity of managing inventory across different locations. When this happens, overstocking or stockouts may occur as a result of failing to balance supply and demand.
Using a centralized dashboard with advanced tracking systems, businesses can gain end-to-end visibility of inventory. Real-time updates enable accurate demand forecasting and efficient inventory management, helping to balance supply and demand.
Prevalence of natural disasters
The Philippines faces frequent typhoons, floods, and other natural disasters that disrupt supply chains and delay operations. Maintaining product availability in such conditions is a persistent challenge, as businesses must adapt to unpredictable weather patterns and often hold higher inventories to ensure readiness. Unfortunately, the tradeoff is increased costs and strained logistics systems.
Creating a contingency plan is essential to mitigate these risks. Here, a feasible solution may be partnering with companies that specialize in safeguarding valuable merchandise and preparing for disruptions like typhoons or similar events.
Lack of digital literacy
The reliance on manual processes and a lack of digital infrastructure hinder businesses from scaling operations efficiently. This gap in technological adoption leaves companies less agile and unable to compete in a rapidly digitizing market.
Training and upskilling the workforce is a critical step in overcoming this challenge. By equipping employees with the skills needed to manage digital tools, businesses can bridge the digital literacy gap and improve operational efficiency.
By adopting user-friendly digital platforms, businesses can integrate logistics operations seamlessly, improving efficiency and accuracy. Providing training and upskilling opportunities ensures employees can effectively manage digital tools, enhancing overall productivity.
Sector-Specific Supply Chain Issues
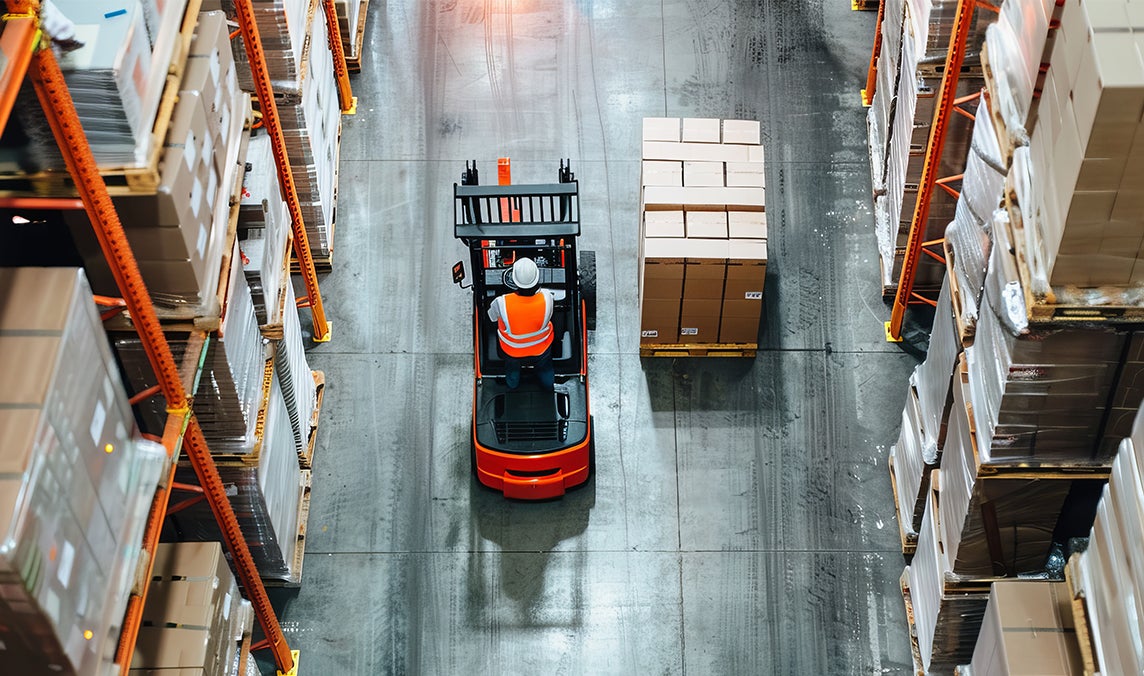
Logistics challenges differ from sector to sector, given their unique operational requirements, customer demands, and regulatory environments. As such, every industry requires tailored strategies to streamline logistics and minimize delays.
The retail sector and last-mile delivery
Retail businesses struggle with last-mile delivery inefficiencies. Even when a customer sees that an item they ordered is out for delivery, it's still possible for the package to arrive late. Traffic congestion often causes these delays in urban areas, while in rural regions, the long distances between delivery stops pose their challenges.
High shipping costs also complicate last-mile delivery. As retailers try to exhaust low-cost courier solutions, customers' expectations for fast and reliable service are not met.
For retail operations, solutions designed for e-commerce sellers and high-volume deliveries can streamline last-mile logistics. These include tools for real-time tracking and route optimization, ensuring packages arrive on time despite traffic or geographic challenges. Integrated reporting dashboards provide visibility into delivery performance, helping businesses identify and address recurring issues.
Moreover, dedicated account managers facilitate smoother communication between logistics providers and retailers, offering actionable insights to refine operations and improve customer satisfaction. By focusing on scalable and efficient last-mile delivery options, retailers can balance cost management with the high service standards their customers expect.
The manufacturing sector and just-in-time (JIT) inventory
It's not uncommon for manufacturers to face hurdles in sourcing raw materials and maintaining just-in-time (JIT) inventory. These delays can halt the assembly of entire product lines. Labor shortages and increased material costs further hamper operations, while natural disasters, cyberattacks, and technological failures add even more burden.
By diversifying supply chain networks and sourcing from multiple suppliers, manufacturers can reduce the risk of total disruption when production cycles or suppliers face delays. This approach ensures business continuity even during unexpected challenges.
The healthcare sector and cold chain logistics
Cold chain logistics in healthcare must maintain precise temperatures, as errors—like broken refrigeration or missing temperature data—can lead to contaminated products, costly delays, and public health risks.
Now imagine a batch of vaccines arriving at a distribution center only to discover that the cooling system failed during transit. The shipment is now compromised.
To address these risks, healthcare providers can adopt real-time monitoring technologies, such as Internet of Things (IoT) sensors and RFID tags. These tools track temperature levels as medical supplies move through the supply chain and provide instant alerts for any deviations, allowing quick intervention to prevent spoilage.
Additionally, partnering with specialized 3PL providers experienced in cold chain management can ensure more robust systems for maintaining consistent quality during transit. 3PL services also typically include liability insurance protection for when unavoidable circumstances compromise the integrity of goods.
The food and beverage sector and its fluctuating demands
F&B businesses and suppliers often encounter a sudden increase in product demand, but repeated loading and unloading can threaten its quality. As such, they are often forced to pay premium prices for inventory, which can erode margins and challenge profitability.
That's why it is paramount for F&B companies to invest in supply chain diversification by partnering with multiple logistics providers, especially those with specialized transportation capabilities.
The Case of Coffee Shop Businesses in the Philippines
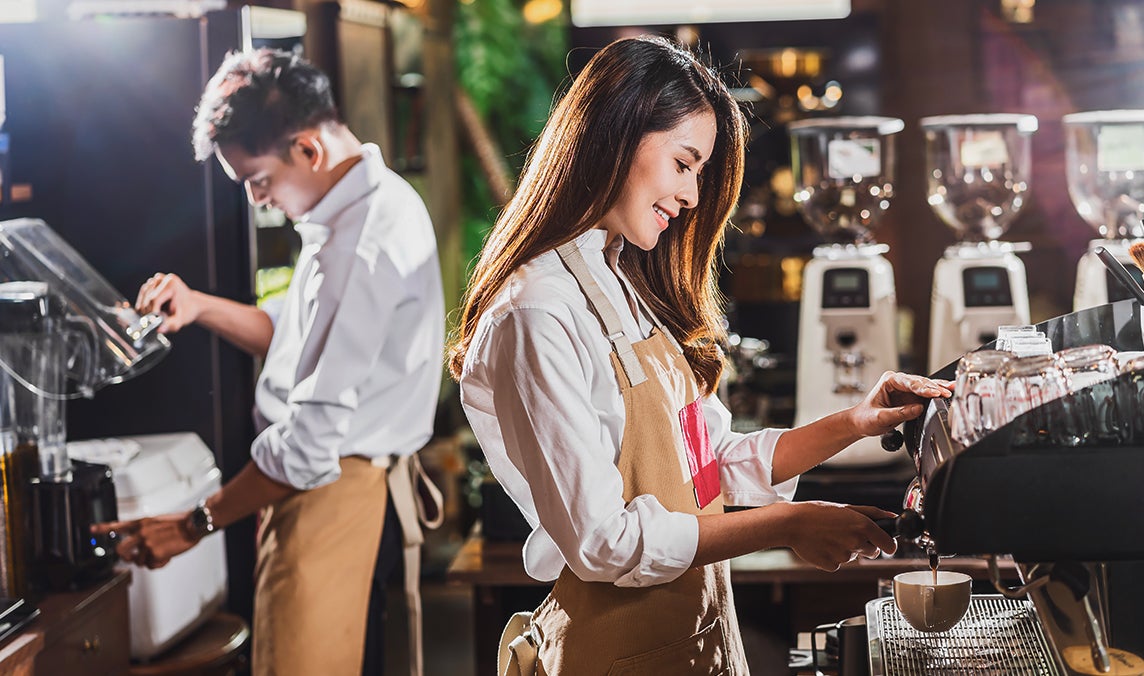
Coffee shop businesses in the Philippines are flourishing, driven by a growing coffee culture and Filipinos' love for social gatherings over a cup of brew. From local chains to global franchises, these establishments have become staples in urban and rural areas.
With the influx of customers frequenting their establishments, coffee shops must keep their operations smooth and efficient by properly managing their daily supplies and inventory.
Logistical Challenges in the Coffee Shop Industry
Frequent supply restocking
Coffee shops need to replenish stock regularly to meet customer demand. This is where efficient solutions like B2B restock come into play. They help businesses manage regular inventory replenishment quickly and reliably.
Managing multiple suppliers
Many coffee shops rely on multiple suppliers for items like beans, milk, syrups, and equipment. Finding reliable coffee shop suppliers in the Philippines is essential to ensure these products' consistent quality and availability despite fluctuating raw material prices.
It should go without saying that ensuring timely and adequate deliveries of coffee shop supplies is a must. Delays or mismanagement can lead to out-of-stock incidents, hurting sales and customer satisfaction.
Seasonal demand fluctuations
Demand for coffee products often varies with the seasons, requiring businesses to adjust their inventory levels accordingly. Overestimating demand can lead to spoilage while underestimating it risks lost sales during peak periods. Fortunately, the right distribution logistics systems can accommodate these fluctuations, offering businesses the flexibility of scaling things up or down in the supply chain.
Limited storage space
Space constraints in many coffee shops make stockpiling inventory challenging. Without efficient supply chain solutions, frequent deliveries become a necessity but can increase costs and complicate operations.
Pickup Coffee x Ninja Van: A Success Story
Pickup Coffee, a fast-growing local brand, faced supply chain challenges as it expanded to over 100 stores nationwide. To overcome logistical hurdles, the company partnered with Ninja Van's Ninja Restock service—a cost-effective and efficient solution for inventory replenishment.
Through this partnership, Pickup Coffee achieved:
- 10% rescued revenue: It saved around 10% of potential lost sales by minimizing out-of-stock incidents.
- 20% operational savings: Efficient stock deliveries helped reduce delivery costs and operational overhead.
- Daily restock efficiency: Ninja Restock handled 4–5 CBM (cubic meters) of inventory daily—a very minimal load requirement—to ensure that supplies were consistently delivered to Pickup Coffee locations all over the Philippines.
Ninja Restock streamlined Pickup Coffee's supply chain by providing a reliable and speedy way to transport goods, allowing the brand to maintain its growth momentum and meet customer demands efficiently.
Indeed, Ninja Van and Pickup Coffee's partnership demonstrates how smart logistics solutions can address common supply chain challenges for coffee shop businesses as they continue to brew success.
Powering Seamless Supply Chains with Ninja Restock
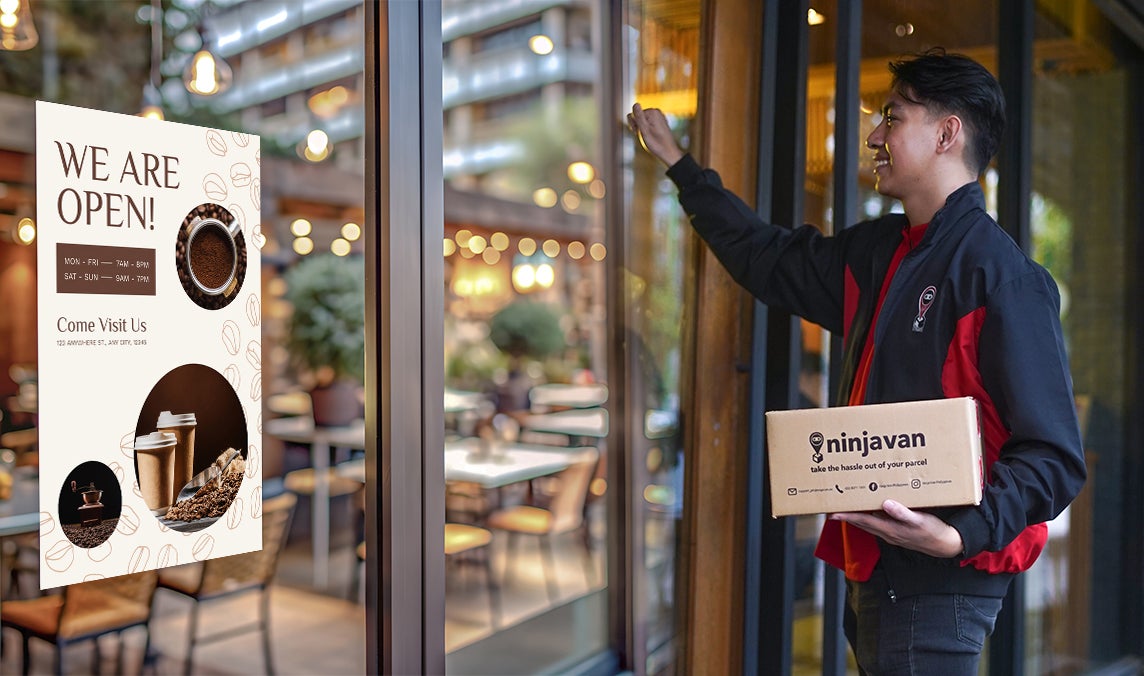
Managing supply chains in the Philippines comes with challenges: high shipping costs, complex customs processes, and industry-specific hurdles like inventory visibility and fluctuating demands. Yet, overcoming these obstacles is possible with the right strategies and reliable partners.
You, too, can transform your supply chain with Ninja Restock's comprehensive logistics solution that focuses on priority handling, speed and reliability, and real-time tracking to ensure your goods are delivered without errors or delays.
When you utilize Ninja Restock's inventory logistics solutions, you can benefit from parcel liability coverage, dedicated account managers, and nationwide coverage for optimal operations and reduced costs. In terms of innovation, Ninja Van leverages advanced technologies like AI to enhance logistics efficiency.
Ready to streamline your supply chain and take logistics to the next level? Explore Ninja Restock's services by visiting the Ninja Van logistics solutions page.
Last but not least, stay connected with Ninja Van! Follow our social media accounts to get the latest updates, tips, and exclusive content!